-
Home
-
Another Nor'easter Again
Another Nor'easter Again
April 4, 2018
Alas, it’s the winter that wants to last, feel the arctic blast, nothing comes to pass.
No fishing, no fun, freezing where I come from, a month of nor'easters after we thought it was done.
In the slow defrost, its hard not to get lost, tossed in the sunlight, fried by the fireside.
Please give me reprieve from the winter that wont leave, snow days, slow days, dreaming of wearing short sleeves.
The Innovator's progress is coming along with a looming deadline of May 15 to go back into the water. The weather is not easy to deal with, but the makeshift barn built on the back of the boat gives shelter against the ongoing streak of nor’easters. It's not necessarily a safe haven, but it keeps the snow off and the rain out for the most part (just don’t stand out there when the wind is blowing 40 NE unless you want to experience the rapture first hand- walls shaking, tarps shivering, the roof wanting to pull off the frame, quite terrifying).
The barn on a boat
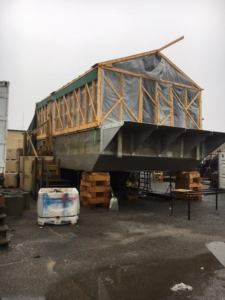
The progress is ongoing, and every day is a new project to tackle. So we take it in stride, and welcome the help of various outside contractors to push the progress along. Pine Hill Equipment from Westport, MA has been a huge help with all the difficulties associated with changing a boat built for salmon farming into a boat for shellfish farming.
For example: we need to run hydraulic winches, a bow thruster, a crane, and electric oyster farming equipment. After looking at the main engine and the clutch, we realized that would be impossible with the existing set up. Back to the drawing board with Pine Hill, and “voila” we have extra engines including an auxiliary “smart” hydraulic pump, and a generator. Problem solved theoretically, now pass it along to ole Adam to figure out how to get them below deck, anchored to the boat, and hooked up in the right places.
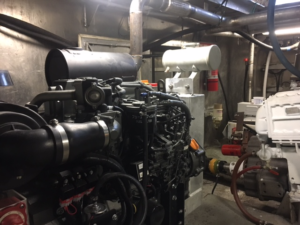
Smart pump only pushes hydraulic fluid when necessary. Note the custom stainless exhaust pipe.
They sent out one of their top welders to cut a semicircle hole in the hull of the boat and weld an aluminum pipe 12” x 4’ back to the boat. There was no defined measurements, just the angle of the dangle to figure out. In a day the hole was cut and the pipe tacked in, another day and he was finished; and the hard part of our bow-thruster installation was complete. The bow thruster is necessary on a boat like this because of its limited maneuverability; a bow thruster helps a boat to position by pushing the front, while the rudder (in the stern behind the propeller) controls the back. The Thomas D. Royal only uses a rudder to steer and because of its shape this is plenty sufficient.
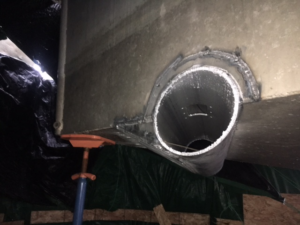
Bow-thruster tube custom weld job.
More help came from down under when the Kiwis made their annual appearance at American Mussel. There was much deliberating on how to install the gantry posts that we received from the New Zealand in 2017, but it was not until Graham and Joe arrived that we got the engineering down proper. These 6” x 6” x 10’ galvanized steel posts will go through the deck and anchor to the concrete hull in specially designed “shoes.” They will also anchor it to the deck with thick aluminum plates before extending 6 feet above the side of the boat (note: the pronunciation of aluminum, and deck are not the same when spoken by these fellows…). Once again its figured out in theory, now pass it along to ole Adam to put it into practice and watch him sweat with the anticipation of May 15!
The list keeps getting longer for ideas on the Innovator because everyone is under the impression that having the boat in our backyard is a one-time deal considering the nightmare that was getting it there. Another reoccurring nightmare comes every time we need to get through the concrete to the bottom of the boat. 6 inches of concrete line the entire hull of the boat for ballast or support. This needs to be drilled, jack-hammered or chiseled out every so often and the task is very laborious.
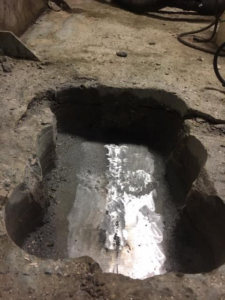
Hole in concrete.
This 6" x 18" x 6" deep hole took about a day to drill, chisel and chip. Needed to fix a crack in the aluminum hull.
The people that we work with are great, full of experience and ideas that keep us moving in the right direction (not always forward, often backwards). For example, Bay View Marine was helping with our stuffing box but had the idea that we should check our cutlass bearing. Sure enough they were dissimilar metals, bronze bearing and stainless shaft, that would eventually corrode one another creating a serious problem down the line. Another project that includes pulling the 20’ long shaft out of the boat which is no easy task. Fortunately it is back in, and done properly to last another 20 years or so. There has been a lot of these holdups, but we are of the mind that sacrifices now will pay dividends later.
So we keep on keeping on, and waiting for those May flowers…